One of the key research-and-education projects of the Institute of Architecture and Construction is the project entitled “Masonry Scaffolds”. Project team is working on development of innovative scaffolds for cast-in-place frame buildings. Nowadays constructors use structures weighing no less than a ton (at that, they are difficult to get transported) or scaffolds made out of materials at hand, which are hazardous for both constructors and people around them. Within the project of students of the SUSU Institute of Architecture and Construction, a principally new concept of scaffolds is being brought up to reality from the scratch and to its practical application: the new scaffolds are lightweight and compact; they are made of durable material and get assembled inside of a building under construction; at that, they are equipped with all the necessary. Project leader, Candidate of Sciences (Engineering), Associate Professor Maksim Molodtsov, and Head of the Department of Construction Operations and Theory of Structures, Candidate of Sciences (Engineering), Associate Professor Grigory Pikus, told us about the project team, the idea and materials, the infrared heater, as well as about other details regarding improvement of scaffolds.
How did the project idea originate?
M. Molodtsov: Our project can be considered a startup. Construction of cast-in-place frame buildings faced the problem of modernization of scaffolds: the weight of traditional scaffolds used to amount more than a ton. A lifting crane used to be needed to transport them. When discussing the project, students themselves proposed the idea to develop lightweight and compact scaffolds that can be carried around by a worker by himself.
Today, the majority of buildings are being constructed upon the cast-in-place frame principle: they have a frame made of columns and solid slabs. When the frame has been assembled, partitions and brick walls need to be erected inside.
For this purpose, until now, constructors of traditional buildings used to use very heavy large-sized scaffolds which are difficult to place inside a building when the slabs have already been installed; getting them out of a building is difficult as well. The optional solution for constructors was making scaffolds out of materials at hand. This is a real problem which can lead to serious injuries among constructors. Besides, transporting of traditional scaffolds always require using freight transport.
What is unique about your scaffolds?
G. Pikus: We propose maximally lightweight, multi-functional and at the same time durable scaffolds. We came up with a solution regarding the material unexpectedly easily. This is the so-called “cellular” cardboard with compressive strength being approximately 0,4 kg/cm2, which allows placing brick-loaded trays on top of it. Global experience shows that cardboard has already started being used in bearing structures, for example, in the walls (Holland), in frames and lining (Germany).
The most important thing is that it is impossible to deliver scaffolds to cast-in-place frame buildings or hybrid precast buildings using a crane: it is impeded by already-erected slabs. Scaffolds that we propose are intended to solve this problem as the crane is only needed to deliver scaffolds to a certain level of a building, and their further placement in one or another part of the floor is carried out manually. At that, they can get easily carried around by a single person and fit into the door frame. They can get easily placed on the steps of a staircase. By their structure, the scaffolds are module blocks that can be combined variably depending on constructors’ goals.
Moreover, the entire load from the scaffolds and the running load (of bricks, mortar or masons) in typical scaffolds is born by two linear supports, which causes considerable forces in a slab, which are not taken into account in the process of designing. It is also necessary to solve the problem connected with ensuring stability of compressed supports. The innovative scaffolds that we propose, the load gets evenly distributed throughout the slab, and there are no separate supports. The block of scaffolds is additionally protected against drenching and damage by carbon fiber.
One of the important advantages of the new scaffolds is the laser level embedded in the scaffolds. Now horizontality and correctness of brickwork layers by the height is going to be monitored by the laser.
.jpg)
The primary material of the scaffolds is cellular cardboard. Compressive strength ≈ 0,4 kg/cm2
Does the block of scaffolds with extended functionality presume special options?
M. Molodtsov: Yes. Specialized versions of the scaffolds presume a block of electronics which includes an infrared heater. Construction is carried out all around the year, and if constructors get frozen, their labor productivity reduces. The idea to put an infrared heater inside the scaffolds was “spied” during trips around Europe.
Infrared heaters there are placed on the ground of street cafes near the tables. There are no walls but people feel warm. We decided to install similar infrared heaters in the improved versions of the proposed samples. The heater and workplace illumination together with light diodes are embedded in the system of the innovative scaffolds.
Moreover, the scaffolds are equipped with USB-charging devices which allow constructors charging their phones and listen to music right at the workplace.
We also propose various models of scaffolding blocks with embedded thermometers for air temperature measurement, a special gauge designated to determine the temperature of a mortar, as well as an electronic display with clock, and even a small refrigerator for water. At that, scaffolds can be bought without the electronic block; the block can be bought separately as an addition to the already-bought scaffolds.
All of this ensures convenience and creates a comfortable environment. The more the convenience, the higher is labor productivity.
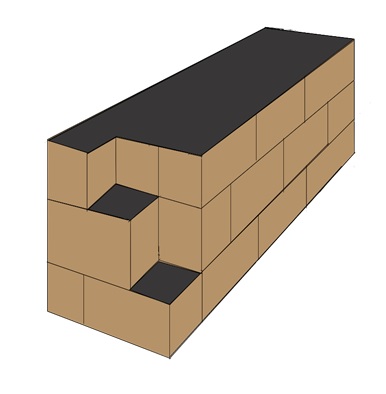
.jpg)
Who does take part in the project?
M. Molodtsov: The project includes five students of full-time mode of study of the specialty 08.04.01 “Construction”. The project group includes the following students of ASI-178 project group: Artem Kolyako, Viktor Gordov, Aleksandr Stenin, Diana Te, Anastasia Nikiforova. The group also includes students who combine working and studying full-time. For example, the author of our presentation is an artist.
The main principle of our work with students is brainstorming. The concept of the innovative scaffolds originated like this, in creative discussions. At the end of May of 2019, we demonstrated prototypes of the scaffolds made of cardboard at a conference on project-based learning as the initial result of the work. The demonstration excited special interest and heavy applause among spectators.
Where are you planning to carry out testing of the scaffolds?
G. Pikus: Testing of the scaffolds is planned to be carried out on construction sites of partner companies. We have many partner companies which might be interested in this. Today constructors make scaffolds out of materials at hand, and this is dangerous. If something happens, responsibility lies upon the leader or developer of the Method Statement. Naturally, these hand-made scaffolds get constructed without any statements; there are no technical provisions for them. In our project, we propose a finished innovative product which allows saving time, money, and health of constructors.